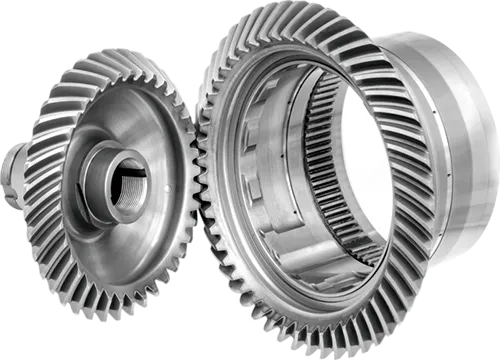
A bevel gear is generally defined as a gear with a conical shape and teeth cut along its conical surface. Two shafts that intersect at a single point are called intersecting shafts. Bevel gears facilitate rotational motion between two intersecting shafts, making them a type of intersecting shaft gear. While commonly known as bevel gears, their umbrella-like shape also earns them the nickname "umbrella gears." They are typically used in devices such as automotive differentials, industrial machinery, and printing machines. Furthermore, the power transmission efficiency of bevel gears is remarkably high, ranging from 98-99%.
The main types of bevel gears include:
With 23 years of experience in custom non-standard gear manufacturing, Kean primarily produces straight bevel gears and spiral bevel gears, achieving a precision level of GB11365-89 Grade 4 (approximately DIN 4-5 / AGMA 10-11).
The transmission efficiency of bevel gears (typically 98-99%) is influenced by several factors:
The key advantages of bevel gears include:
Bevel gears are indispensable in numerous industries:
Straight bevel gears have straight teeth that extend radially along the pitch cone. These are the simplest type of bevel gears and are typically used in low-speed applications, such as gears in printing equipment or bevel gears used in vehicle differential mechanisms.
Spiral bevel gears feature curved tooth surfaces. Compared to straight bevel gears, they provide smoother meshing and significantly lower noise operation.
Contact us today to customize high-precision gear transmission parts for your specific needs!
At Kean, we utilize advanced equipment such as Gleason Phoenix 275G/800G CNC spiral bevel gear grinders and ZEISS coordinate measuring machines to produce bevel gears with a precision rating of GB11365-89 Grade 4 (approximately DIN 4-5 / AGMA 10-11). This ensures highly efficient power transmission, serving critical industries like aerospace and automotive.